Welcome to Gainesville, BOD3
UF’s newest printer can build homes, sea walls and careers
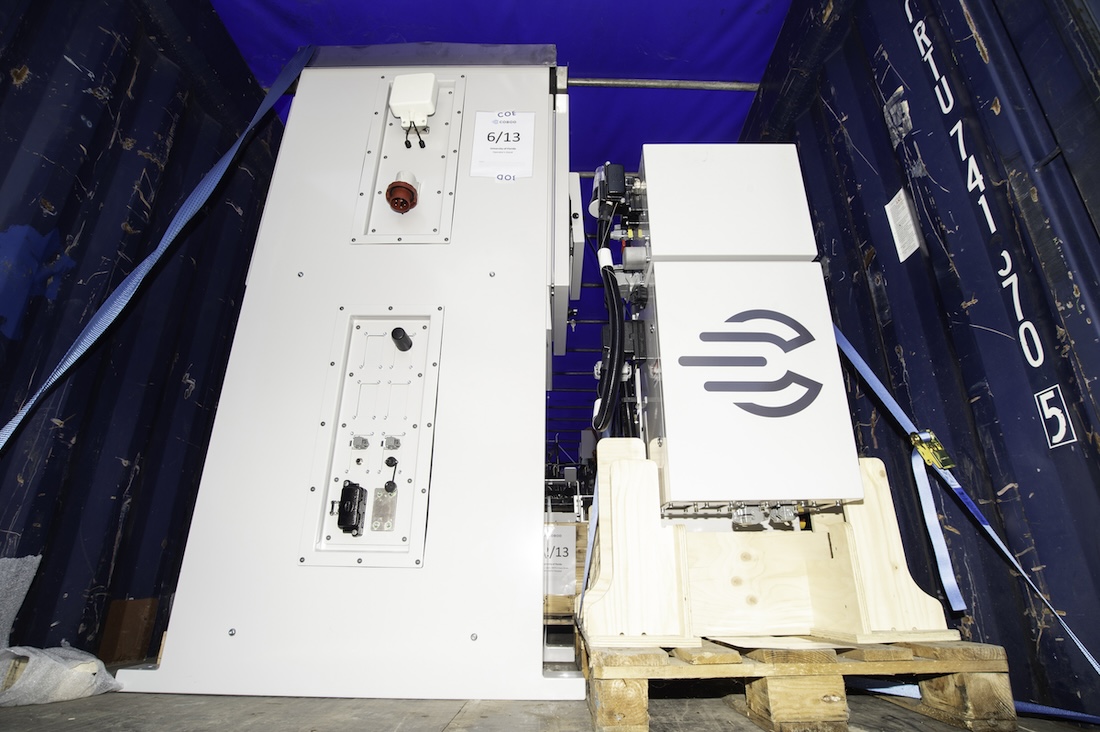
After a journey from Denmark, the primary components of the BOD3 3D construction arrived Friday at the University of Florida’s East Campus. Photo by Dave Schlenker
One of the country’s largest and most-advanced 3D construction printers – as in a printer that makes homes – has crossed the Atlantic Ocean and arrived at the University of Florida.
Manufactured by COBOD International in Denmark, the two-story printer was shipped in pieces to the Port of Savannah in Georgia earlier this month. It cleared U.S. Customs and pulled into UF’s East Campus in two semi-trucks Friday morning. It eventually will live in “The Pit” (Weil Hall Structures and Materials Lab), a large industrial space in the Herbert Wertheim College of Engineering on the main campus.
Make no mistake, UF’s new BOD3 is a big deal in size, scope and significance.
This is COBOD’s newest 3D construction printer, the first of its new third-generation models sold in the United States. The primary three elements – mixer/cement silo, concrete piston pump and the 3D printer components – weigh 27,000 pounds, collectively.
“The opportunities for the interplay of artificial intelligence, machine learning, data analytics and smart manufacturing will be one of a kind in the country,” said UF Professor Iris V. Rivero, the chair of the UF Department of Industrial and Systems Engineering who launched the effort to secure the 3D printer. “With UF’s access to the Space Coast, vast areas of shoreline, and infrastructure needs, we will be the hub of innovation in Industrial Manufacturing Construction Engineering.
“UFs Industrial and Systems Engineering department will lead the path defining one-of-a-kind, infrastructure-driven interdisciplinary research and education,” she added.
The printer will be incorporated into curriculum for multiple departments in the College of Engineering, including lessons and projects in construction, manufacturing, materials, data analytics and operations research, structural health monitoring, coastal resilience, safety, design and sustainability.
UF’s College of Design, Construction and Planning, or DCP, offers an advanced construction technology course dedicated to teaching students about the fundamentals of 3D printing, including material selection, design processes, and printing techniques, noted Joey Mazzaferro, the college’s associate director of communications.
The development of DCP 3D printing course is supported by a successful NSF proposal with a focus on construction — the first of its kind at a university — demonstrating a forward-thinking approach to incorporating advanced construction technologies into the curriculum, said Chaofeng Wang, assistant professor of AI in the Built Environment at UF's M.E. Rinker Sr., School of Construction Management.
“We are collaborating with the College of Engineering to expand this course, reaching more students interested in these innovations,” said Wang. “The acquisition of this new 3D printer will bridge the gap between classroom learning and real-world industry experience, while also driving research in additive manufacturing, material science, and construction automation.”
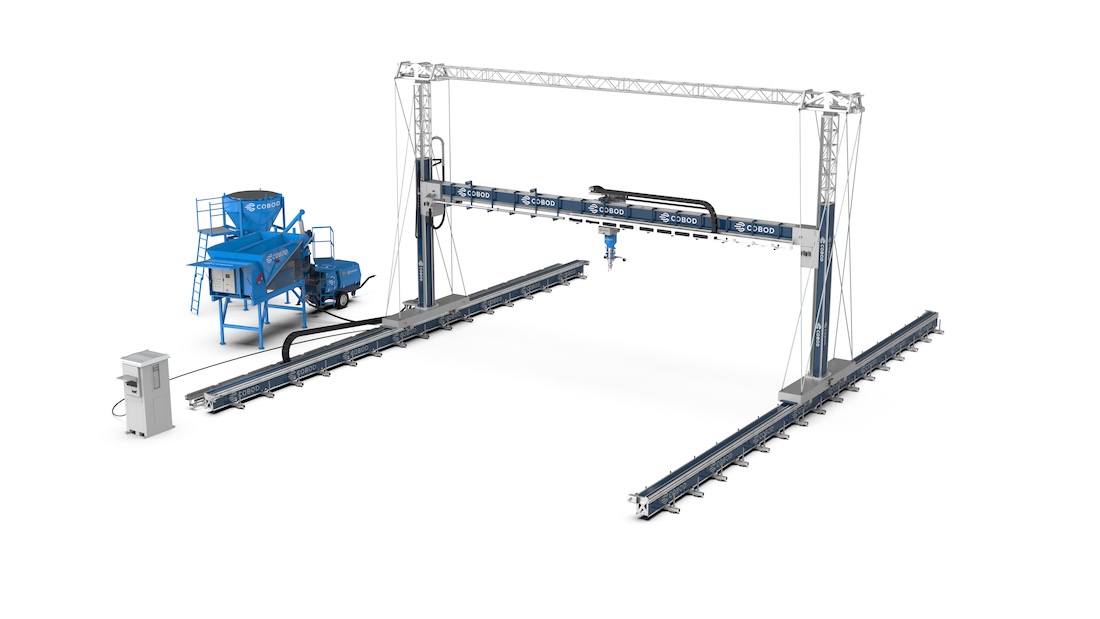
This illustration provided by COBOD international shows all the components of the BOD3 once assembled.
Aladdin Alwisy, an assistant professor in the Rinker School of Construction Management, said the technology has the potential to become a viable alternative to traditional concrete and steel construction.
“We aim to enhance the quality, speed, and applicability of 3D-printed structures for various building types and heights,” he added.
Forrest Masters, Ph.D., interim dean of UF’s College of Engineering, looks forward to seeing the printer’s impact on curriculum, research, and tangible industry outcomes.
“The addition of this cutting-edge equipment will distinguish UF from its peers by offering unique experiential learning opportunities,” Masters said. "UF remains at the forefront of addressing industry needs, and through the introduction of our new Industrialized Construction program, the 3D printer will exemplify the latest advancements in technology aimed at addressing critical societal challenges."
While new and relatively rare in the United States, 3D printing in construction is gaining ground in the industry. The machines print structures by layering rows of wet concrete with a nozzle moved by an overhead robotic arm – back and forth, one layer on top of the next to create walls.
Proponents contend 3D construction printing is faster than traditional construction, produces less material waste and is more cost effective. Some companies report homes built within weeks with a handful of workers on site to run the machine. COBOD reported the company 14Trees built 10 houses in 10 weeks with its BOD2 model in Kilifi, Kenya, from October 2022 to January 2023.
“Beyond the clear societal benefits of cheaper, faster, and higher-quality buildings and infrastructure, the automated prefabrication system will also improve the working conditions of construction workers by significantly reducing physically demanding and hazardous tasks,” Alwisy said.
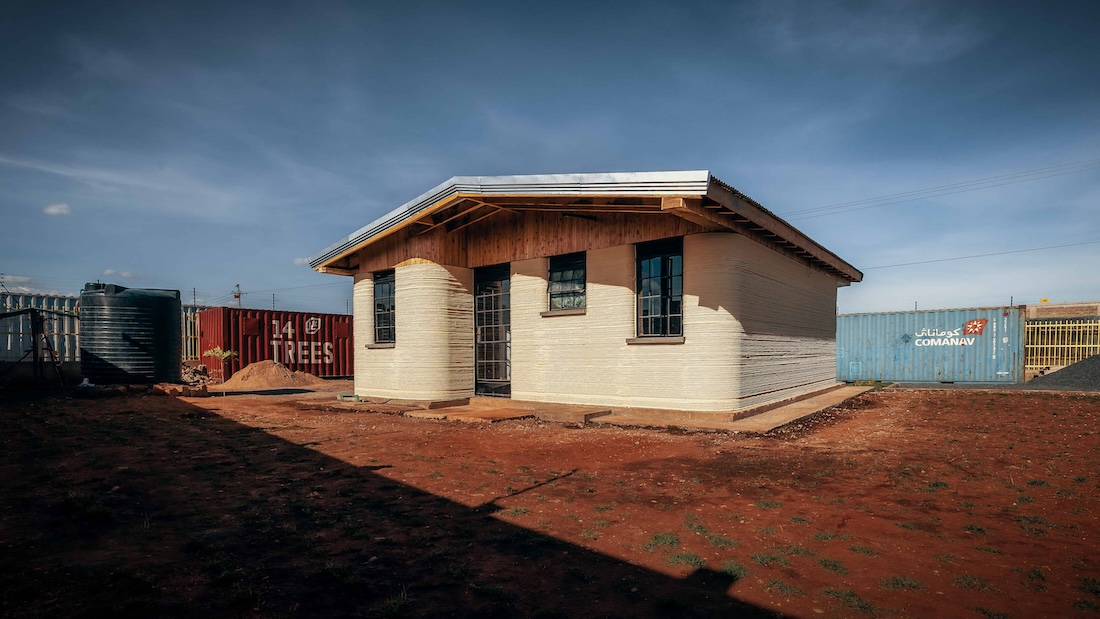
This is an example of a home built by a COBOD International 3D printer. Photo provided by COBOD International
There are several printer manufacturers and vendors who do business in Florida. Printed Farms in South Florida used a COBOD model to build the state’s very first 3D-printed home, which is in Tallahassee.
“We have a customer at a large Air Force base in Florida. In addition, our customer, 1Print (in Broward County), is using our technology to 3D print various structures, including coastal barriers,” noted Philip Lund-Nielsen, co-founder and head of Americas for BOD International. “We collaborate with many universities for research grants, including NSF, printer deployment, lectures and building programs.”
In April, COBOD and the University of Miami School of Architecture opened a 3D printing hub, equipped with the BOD2 construction printer in Miami. UM’s printer rivals the size of UF’s printer but has the capacity to go larger if needed.
UF’s printer is one of the Presidential Strategic Initiatives, which allotted $2.5 million over two years to “help harness the power of digital design, AI, and robotic automation to enhance productivity, safety, and quality in residential and commercial construction.”
Additional funding came from a $1.5 million grant from Autodesk, a California-based software company for design, construction and engineering.
There has been significant interest in 3D construction printing to ease home prices and enhance sustainable housing. ICON, a printer manufacturer in Texas, built six houses for homeless residents in partnership with Texas nonprofit Community First. The first resident of a 3D-printed home in the country, in fact, was a 73-year-old former heroin addict restarting life in 2020, according to a 2023 report on “60 Minutes.”
“The growing demand for sustainable and eco-friendly construction practices is a key driver of the 3D printing construction market,” SNS Insider Research reported this month. The market research company contends the 3D construction market was valued at $36.7 million in 2023 and is expected to reach $20.56 billion by 2032.
And at UF, the BOD3 will go well beyond making walls.
“Within the next two to five years, the 3D printer is anticipated to become an integral component of an automated prefabrication system alongside other robotic technologies, such as industrial robotic arms, mobile robots, legged robots, and collaborative robots,” Alwisy said. “This automated setup will expand the 3D printer's applications beyond building structures to encompass a wide range of tasks supporting substructures, shells, MEP systems [mechanical, electrical, and plumbing], and finishing work.”